Hello friends, Today you are reading about Injection Molding Machine, which means you have some ideas about it. And you have doubts also like, What is the Injection Molding Machine? What is the working principle? And What are the applications of this machine? We will discuss all the things in this post. Let, we will discuss the details.
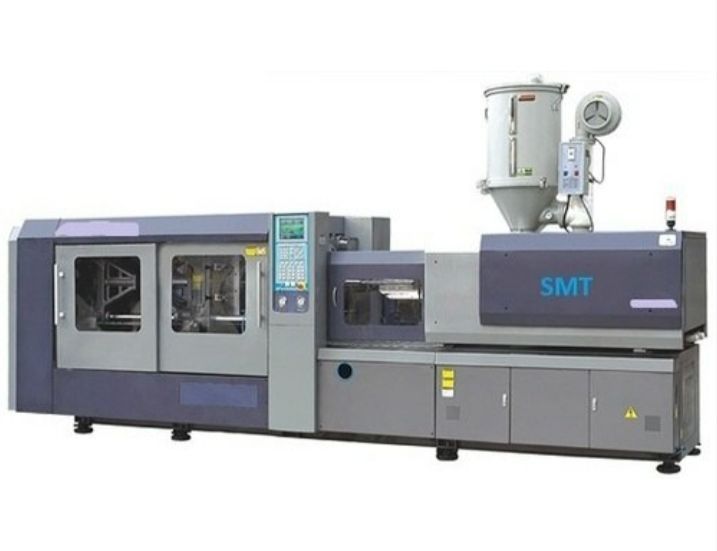
Image source: SMT Plastic Injection Molding Machine
As per the name, it is used in the moulding process. Moulding (Molding) is a manufacturing process, in which a liquid or malleable material is shaped by using a solid frame. This solid frame is a Mould. We will read details about mould in our next article. In this molding machine, molten plastic is injected through a reciprocating screw and barrel (or we can say a syringe) into the mould. Therefore, this machine is called an Injection Moulding machine. After then cooling is provided for the solidification.

Image source: Bosch Rexroth
Today, Injection Molding is inevitable in plastic processing. This machine is used for the mass production of plastic products. There is a wide range of plastic products is available in our daily life. From our toothbrush and toothpaste tube’s cap to pen and pen’s cap to Medicine bottle cap and so much. This list is endless. Also, this process is used on glass and thermosetting polymers.
So let’s, first, we will see the basic parts of an injection moulding machine.
Page Contents
Construction of Injection Moulding Machine:
These days, modern Injection machines consist of the following basic parts:
- Feeding Hopper
- Extruder Screw and Barrel
- Injection Chamber
- Mould Clamping Mechanism – An arrangement for applying pressure to the moulds.
- Fixed and Moving Plates
- Control Panel – NC or CNC
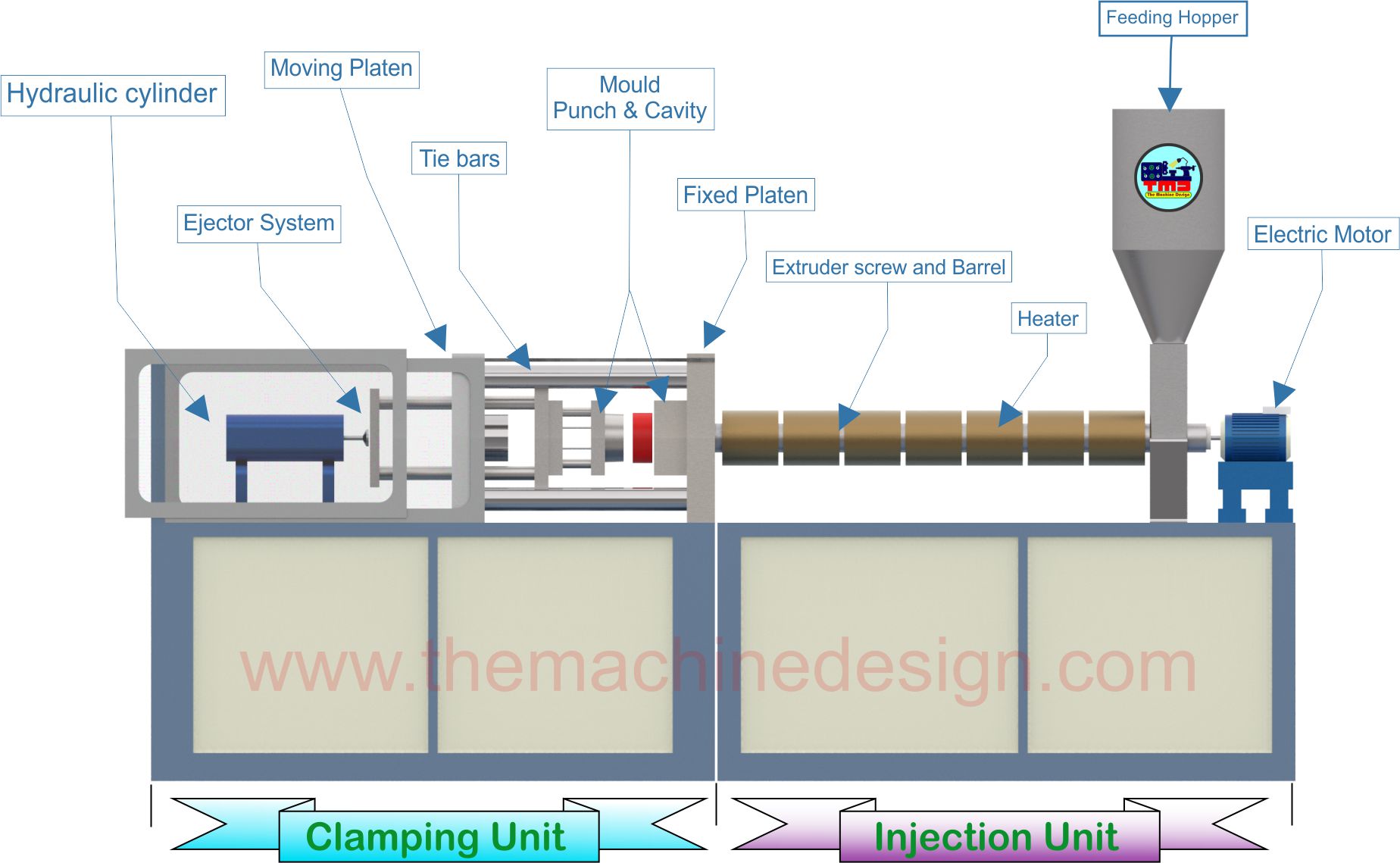
1. Feeding Hopper:
A conical container at one end of the machine. It looks like a funnel. It is located at the barrel’s inlet end. This hopper holds and charges the raw plastic resin pallets material. It is an entry point for plastic material. Feeding hopers are made from steel or stainless steel. It looks like inverted pyramid or conical container. It discharges raw plastic from it’s bottom as per the required. The size of hopers varies according to machine sizes.
Also Read:
- What is Wrench and Its Uses?
- Hydrogen Fuel Cell Cars: A Closer Look at the Technology
- Working Principle, Main Parts and Operations of Lathe Machine.
2. Extruder Screw and Barrel:
The Extruder screw is located inside the barrel. The plastic resin pallets come into the barrel from the hopper. A heater applies heat to the barrel for melting the plastic. A variable speed electric motor rotates the extruder screw from one end. This screw has threads. These are looks and act like flutes on a drill bit. These threads provide motion to plastic granules. The extruder screw pushes the molten plastic into the injection chamber.
The extruder screw’s threads have three sections in length. As you can see in the image, the first section is the feed section, where the granules come from the hopper. The second section is the compression section in the middle of the length. The plastic resins are heated and compressed in the middle section. And the last section is the metering section. This section is also known as the pumping section. Here raw material (resin) is heated and mixed properly. This molten material becomes a homogeneous mixture at this stage.
The end of the screw has a non-returning valve. The check valve is another phrase of this valve. This valve prevents to flow of reverse molten material during the extrusion stage.
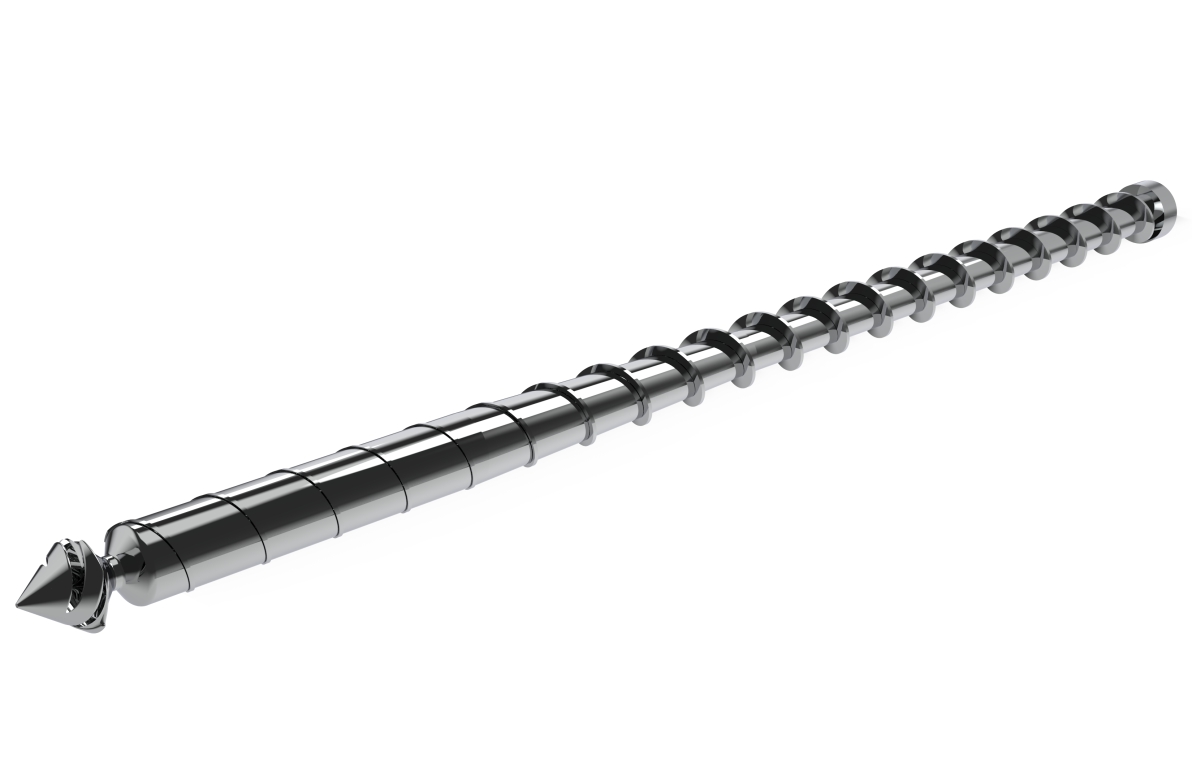
3. Injection Chamber:
The whole assembly is just what we have read in the above paragraph, i.e, the Extruder screw, barrel and heaters assembly is an Injection chamber. Here the material is injected inside the mould.
4. Mould and Clamping Mechanism:
A mould is a tool, in which melted plastic takes a shape after solidifying. A cooling system inside of the mould helps to solidify the plastic material quickly. Basically, the moulds have two halves. The moving plate carries one half and the fixed plate carries another half.
A clamping mechanism provides appropriate pressure to the mould plates during the injection cycle. The pressure created during the injection process on the moving plate in the rearward direction. So it tends to open the mould. Usually, the hydraulic actuators actuate the clamping mechanism.
Also Read:
5. Fixed and Moving Plates:
The fixed plate is located on the injection chamber side. And on the opposite side, the clamping mechanism moves the moving plate. Mould’s one part is mounted on the fixed pate and another part is mounted on the movable part.
Now I have a question for you. Which one part of the moulds should be mounted on the fixed plate and another on the moving plate? Please mention your answer in the comment section. I will answer this in our next article.
6. Control Panel:
The control panel is a part of the Machine. A machine operator operates the machine using this control panel. Some machines are controlled by using NC and some CNC. NC, Numeric Control is an older technology and CNC, Computer Numeric control is the latest one. What is the difference between NC and CNC? For this answer please check our next article.
Working of Injection Molding Machine:
Injection Molding Machine Process:
As the name shows, an injector charges the molten material inside the mould. And this mould makes a finished OR semi-finished product. Now, Let we will see how this Machine Works?
Raw plastic material is filled into the hopper manually or by feeding devices. The base plastic granules, coloured and additive granules mixture make the complete raw material. This material goes down into the barrel due to gravity. The barrel or cylinder is surrounded by a heater throughout its length. That heater is used to melt the raw material. Here, inside the barrel, a screw carries these moult. It pushes the molten material towards the mould with a large amount of pressure. That is located on the end of the barrel.
This mould having usually two halves. One half mounted on the fixed plate, at the end of the barrel. And another one mounted on the moving plate. A hydraulic or pneumatic mechanism applies pressure on the moulds. It opposes the injection pressure. This force is measured in Tons.
What is Clamping Force?
A force is needed to hold the mould closed during the injection, that force is Clamping Force.
Now, the part/s inside the cavity is cooled by a cooling system for solidification. Usually, a liquid cooling system is used for cooling. This solidification happens within a few seconds. After that, mould halves open by unclamping. And then stuck part ejects by ejection system without damaging the part. Ejector pins and ejector plates are used in the ejection system.
An injection moulding machine performs this action very fast, frequently and automatically.
Affecting Parameter in Injection Molding Process:
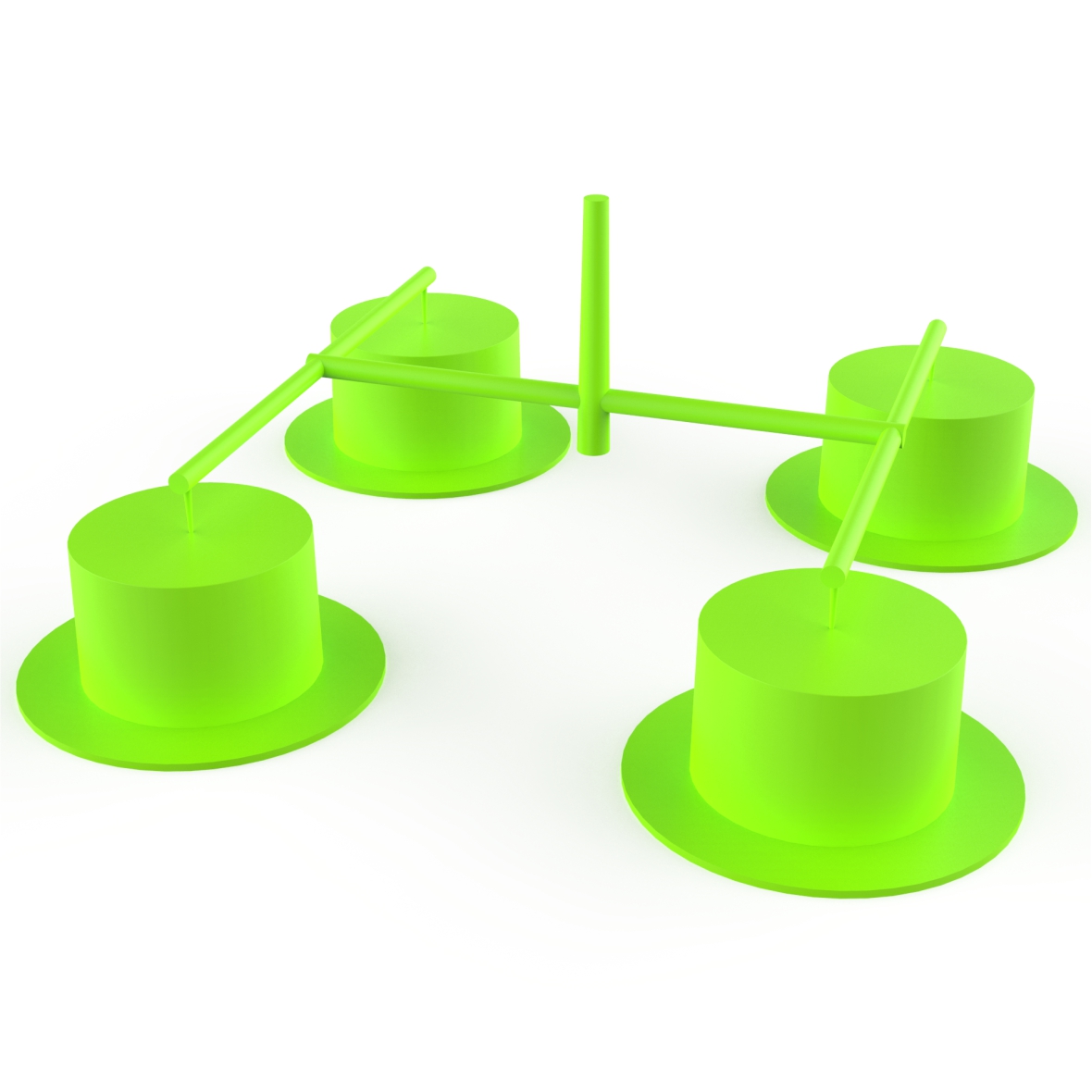
The moulding process affects by the following parameters.
- The heating temperature of the moult
- Mould Temperature
- Injection Pressure
- Injection Time
- Packing pressure
- Packing Time
- Coolant temperature
- Cooling Time
- Injection Capacity of machine
Also Read:
Applications of Injection Molding Machine:
Moulding machines are used to manufacture plastic products in mass volume. There are lots of fields where plastic components are useful. As we can say this list is countless. Of course, From our daily life products like crockery, cutlery, cookware, furniture etc. It is used in various industries, like Automotive, Aerospace, Marine, Machinery, Medical and so on. For more information, please stay tuned…
FAQ’s:
[sp_easyaccordion id=”899″]
This is exactly what I needed today. Thank you for the valuable information!
Hello, my employer just received a sizable order for bespoke plastic components from a significant client, thus he is looking for plastic injection molding companies. The volume is above the capacity of our existing manufacturing setup, and we cannot afford to lose this chance. I’ll let them know that this equipment is utilized to mass-produce plastic goods and that injection molding is a need in the processing of plastic.